Behind the Scenes: UAS Taking Flight
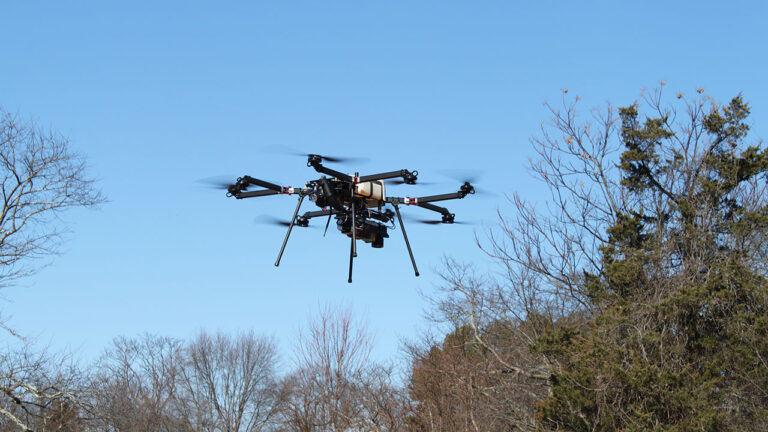
In this new blog series, I want to combine my love of writing with the learning opportunities I get in the field and give you a behind the scenes look at the work we do! For the first edition, I thought it would be fitting to dive into something that can be used on a variety of projects.
Recently, I was invited by the UAS team at headquarters to watch the test flight of a new drone for our fleet. Prior to joining Colliers Engineering & Design, I have only worked with drones for videography. I never knew they could be used for a variety of projects, from surveying to building inspections! There was so much I got to learn at the test flight, so let’s dive into it.
Firstly, the word drone is only one part of the technology. Most industry professionals, pilots and the Federal Aviation Association (FAA) tend to use other terms like Unmanned Aerial Vehicle (UAV) or Unmanned Aerial System (UAS), which is what we use at CED. The use of the word systems allows for the accounting of the vehicle, flight team, and other components that enable it to collect the data needed.
According to FAA’s Small UAS Regulations (Part 107), pilots are required to avoid manned vehicles, such as planes; keep a visual line of site (VLOS) on the aircraft, either by the pilot or a visual observer; and can only fly up to an altitude of 400 ft without having to secure a waiver from the FAA. The pilots at CED are also all licensed under this rule with the FAA and carry their certificates as well as the vehicle’s registration on them during flights.
When it comes to collecting data, there are different types of sensors that can be deployed from the aircraft. These sensors can include photo and video cameras, infrared cameras, LiDAR (or light detection and ranging sensors, a remote sensing method that uses light in the form of a pulsed laser to measure ranges (variable distances) to the earth.), magnetometers that measure magnetic fields, multispectral sensors for collecting wavelengths of light, and gas detection sensors. At CED, we have an assortment of job-specific aircraft and sensors that are applied to a wide variety of projects from mapping large project sites to bridge and tower video inspection.
Before Departure
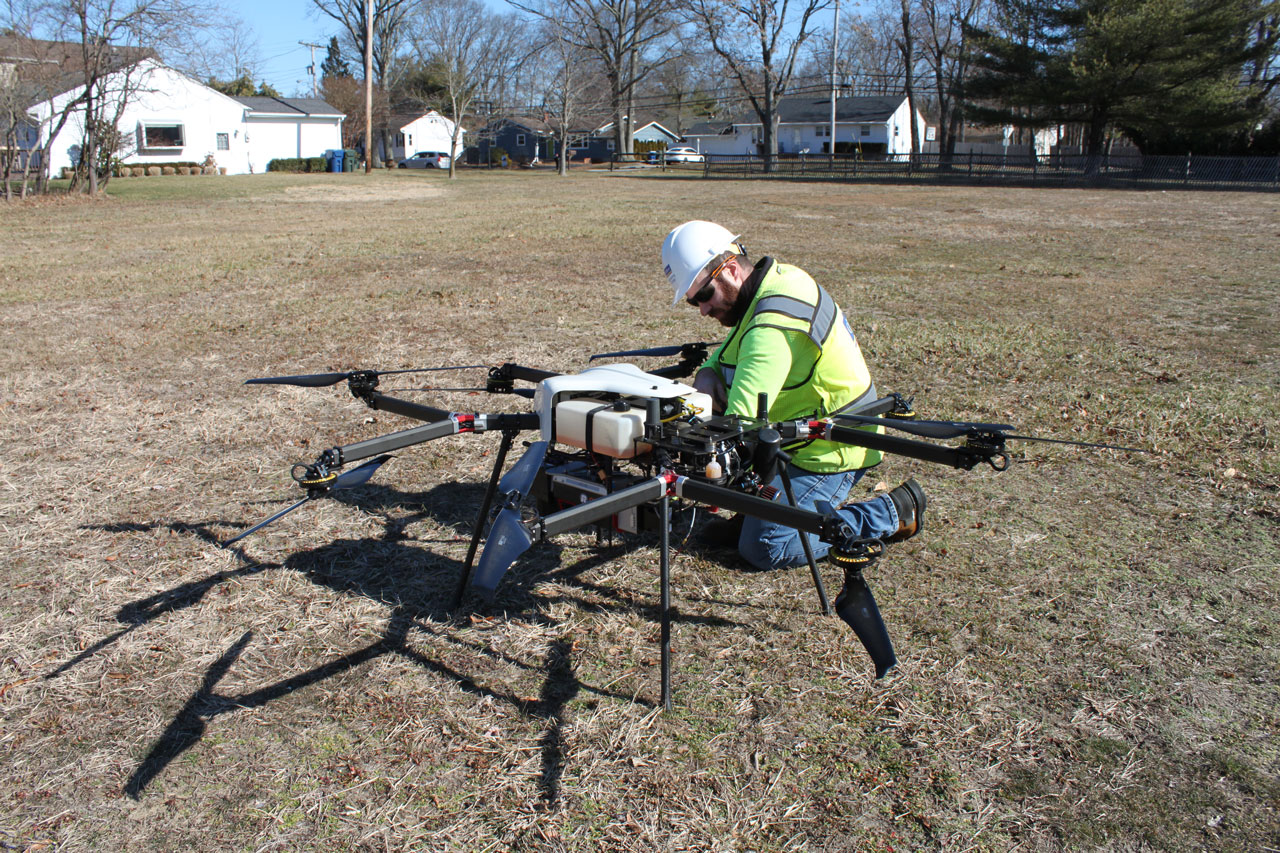
Brian Willig, CST Office II, is inspecting the aircraft before takeoff.
Much like airplanes, certified UAS operators are required to complete a pre-flight inspection. Since every aircraft is unique, it is important for the field crew to make sure there is no visible damage to the aircraft. Generally, inspections include making sure any screws are tightened down, batteries are charged (if appropriate), inspection of the aircraft exterior and propellers for any damage and making sure the motors are properly working.
They also must be aware of weather conditions before takeoff. According to Brian Willig, Senior UAS Pilot from CED’s headquarters, most of the vehicles in our fleet are not waterproof or water resistant, so pilots are always watching the weather closely before flights, as any kind of rain, fog, or snow will push a flight back. Wind is also another major player, especially for safety of the crew. Winds over 25 mph can interfere with the vehicle’s payload and lower data quality. If the flight is collecting photos, Willig says it is best to do it on an overcast day rather than a bright and sunny one due to the shadows!
Temperature is also another factor taken into consideration when preparing for a flight. Depending on if the drone operates on gasoline or electric, temperature will affect the power consumption and operation times will fluctuate. According to the standard operating procedures for CED, all battery-operated aircraft must land with a minimum of 20% power remaining. Willig says most of CED’s fleet can operate in temperatures ranging from 14 degrees to 114 degrees!
The last thing our certified pilots must consider before takeoff is air space. Legally, UAS cannot be operated anywhere near clouds. The FAA states that all drones must be at least 500 ft below and 2,000 ft away horizontally away from clouds. If you are flying near an airport, Willig says pilots typically coordinate with the local Air Traffic Controls. There are also online services, such as UASidekick, that can help coordinate operation in airspaces where special permissions are needed.
3, 2, 1… Take Off
After all the preparations are complete, it is time to fly! Depending on what type of data is being collected and the vehicle’s payload, the field crew will put targets on the ground to assist in the data capture. These targets, according to Willig make it easier to correct data after a flight, keeping all the data aligned in the process. On sites that are 100 acres or less, five targets are used – one in each corner and one in the center. There are a variety of target options including vinyl targets and painted targets with patterns, but permanent items at a site can also be used as targets such as edges of parking lots and corners of concrete slabs.
Both remote pilots and crew members must wear personal protective equipment (PPE) while actively working on a job site. Depending on the time of year, PPE can include a high visibility shirt, vest or winter jacket. All crew on the scene must wear long pants, steel toe or composite toe work boots, and a hard hat for safety for the entire duration of the flight.
Pilots aren’t the only ones who have an important job on the scene. The FAA recommends that at least one person, designated as a visual observer, must keep a visual line of sight on the aircraft while helping the pilot steer clear of any obstructions such as buildings, telephone poles, wires, and trees. The operator of the vehicle, or the Remote Pilot-in-Command, will let the visual observers aware of the aircraft’s movements so they can confirm them. Communication is key during flights.
UAS flights are also rather short, with Willig saying that the average length is around 20 minutes in air. The amount of time on the field and in the air depends on the type of data being collected and the vehicle itself, with our larger aircrafts able to fly for as much as 90 minutes.
Prepare for Landing
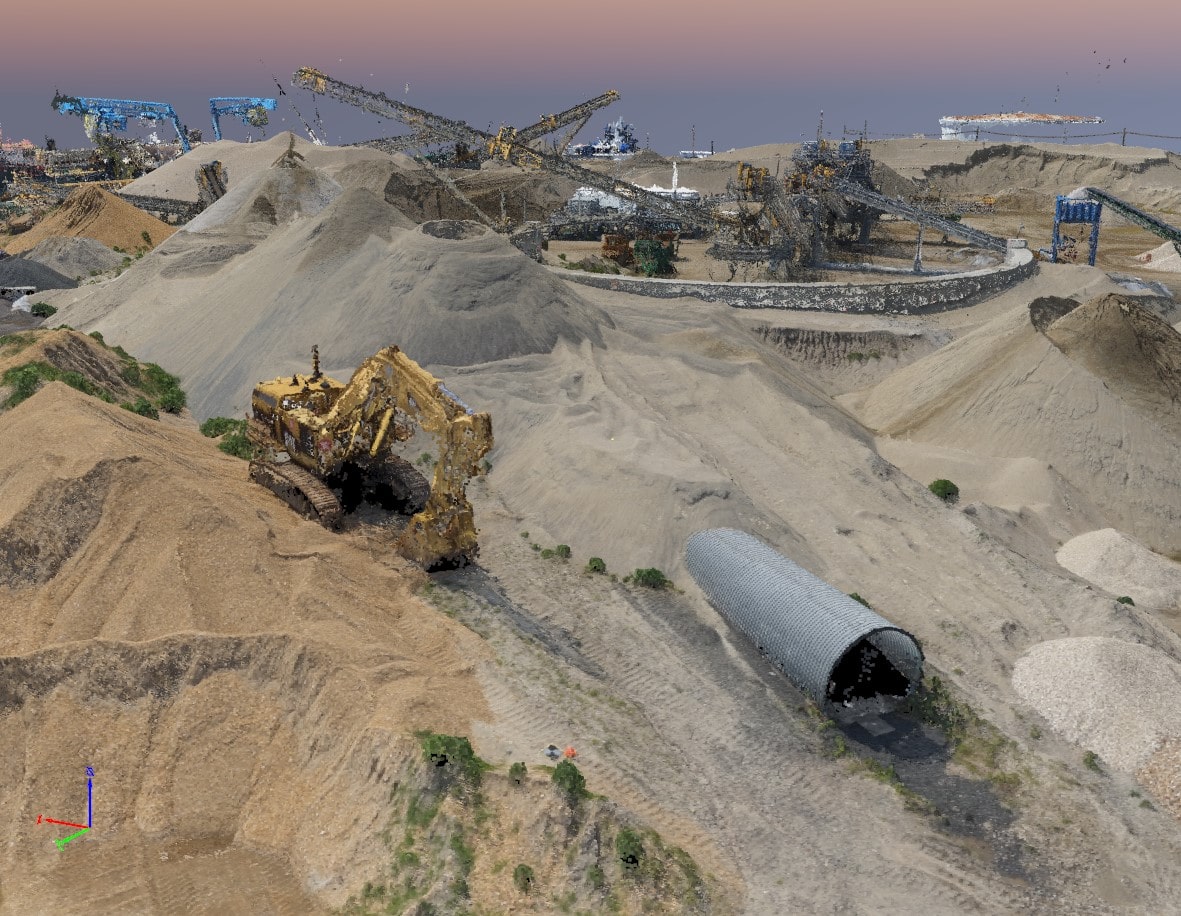
An example of a deliverable a client receives includes this soil model used to measure the pile volumes.
Now, it’s time to get the vehicle back onto the ground, transfer the data, interpret it and make it ready to send it off to clients. Before the aircraft even takes off, a landing zone is established by the crew. This zone should be clear of any tall obstructions, such as trees and buildings. It should also be close to the base station, where the aircraft was assembled and will be taken apart.
Once the vehicle comes down, no one goes near it until all the motors are off. Despite their small size, the aircraft propellers and motors can be super dangerous! When everything is powered off, the crew will begin taking it apart. Fun fact – the aircraft is disassembled in the reverse order of assembly to make sure all parts are put back in a certain way!
Our UAS team then transfers all the imaging collected to the data extraction team, who ensures the data is turned into a deliverable made to the client’s specification. Just like in photo and video editing, the team has the responsibility to make sure everything looks perfect; no weird images of the team on the ground, edits to pixilation and removing cars are just some of the tasks at hand. Most of the data gets transformed into topographic maps, but the team can create as-builts, American Land Title Association (ALTA) boundary surveys, assist in inspections, and more! According to Willig, approximately 90% of the work he and the team done are topographic surveys.
Conclusion
I was amazed to see how the entire process worked. I am grateful to our team on-the-scene for allowing me to ask so many questions and photograph the event.
Special thanks to Brian Willig, Geoff Giullini, Joe Hammel and Jay Ambrust for inviting us to this test flight! I am so lucky to continue to learn about the work we do out in the field. Here’s to hoping I get invited to another worksite!
Comments are closed.